
The objective of this work is to show that by optimizing the solidification pattern, i.e., establishing directional and progressive solidification with the help of the Niyama criterion, macrosegregation and hot tearing issues can be both minimized or eliminated entirely.

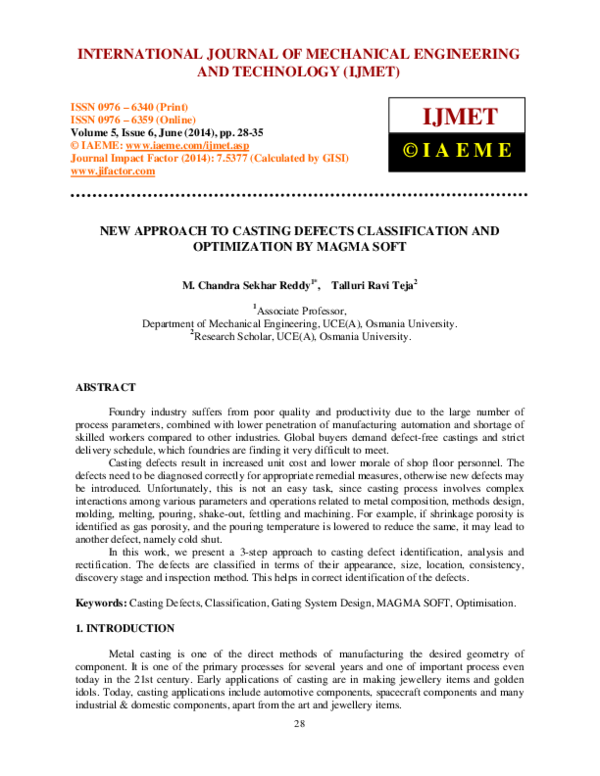
The physics behind macrosegregation and hot tears indicate that these two defects also are dependent heavily on thermal gradients and pressure drop in the mushy zone. The tendency of forming centerline porosity is governed by the temperature distribution close to the end of the solidification interval, specifically by thermal gradients and cooling rates. Still, the remaining porosity indication in MAGMASOFT ® was critical enough to reject the cast part in some cases of application (Fig. 1).A methodology of how to exploit the Niyama criterion for the elimination of various defects such as centerline porosity, macrosegregation, and hot tearing in steel castings is presented. Based on the results, the experts decided on the next changes, and this process was repeated.Īfter running 25 different versions manually and investing two weeks of work, the simulation results showed a decrease of the porosity level. Each version was prepared, simulated and analyzed. Different layouts and feeder sizes were tested in the traditional approach: changes were decided upon by the experts up front. A redesign of the feeding system was necessary to solve the porosity problems and improve the quality. With an initial feeding system design selected manually, the cast part showed a significant level of porosity defects.

A suspension part with critical safety requirements was used to virtually evaluate the robustness of the process design and compare the outcome with the sequential step-by-step simulation approach used until then. Achieving the specifications for internal soundness is crucial to avoid the component failing in the field. Most ductile iron parts have tight quality requirements.
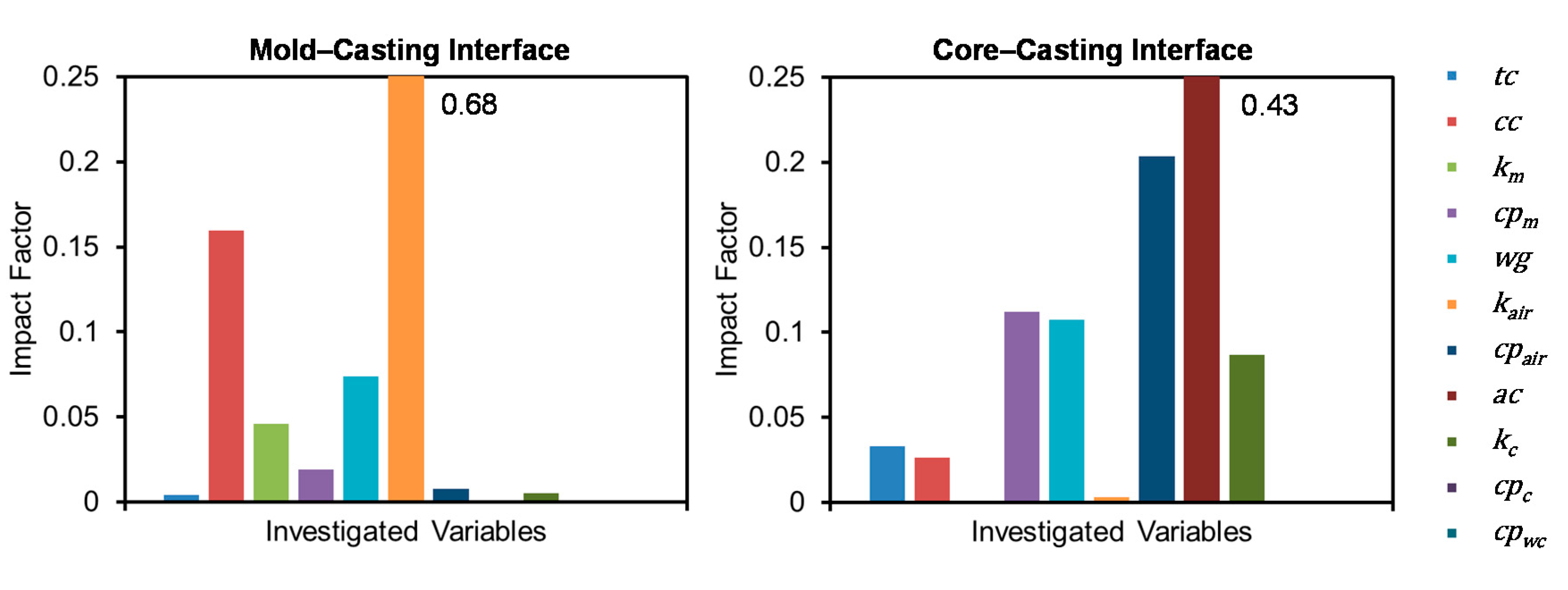
The outcome was more than convincing: it is possible to get better results in less time. In order to achieve these goals, Schulz in Brazil started using the MAGMASOFT ® capabilities for Autonomous Engineering and compared it with its traditional way of using the simulation tool. To keep the business profitable, the solution also has to be a suitable compromise between quality and cost. Moreover, the project design has to guarantee robust quality despite the process variations typical on the shop floor. Success in the foundry market today not only depends on a good gating and risering design and a resulting good quality part.
